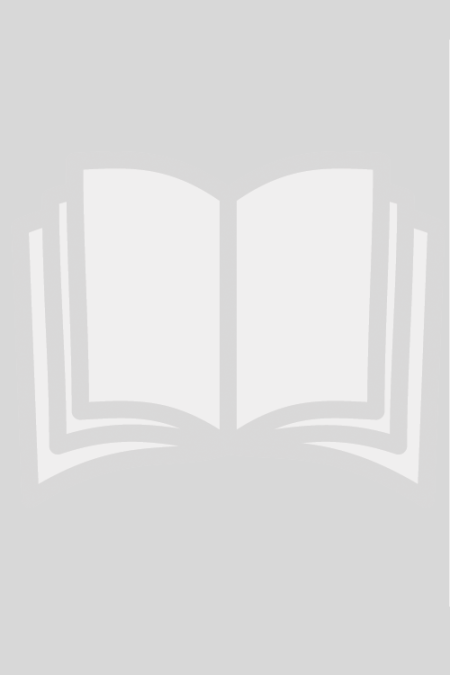
Jipm-japan Institute of plant maintenance
Miglioramento specifico con il TPM
Il terzo volume della serie "Comprendere bene il TPM" (o miglioramento specifico). Come effettuare l'analisi dei guasti; come ridurre i tempi di attrezzaggio; come eliminare le microfermate; quali provvedimenti prendere contro le perdite di velocità. Per ciascuno degli argomenti trattati viene fornita una traccia pratica che conduce passo passo alla soluzione del problema.
Pagine: 126
ISBN: 9788820498757
Edizione: 2a ristampa 2023, 2a edizione 2008
Codice editore: 563.50
Disponibilità: Discreta